Business
- HOME
- Business
- Special Heading Parts
Special Heading Parts
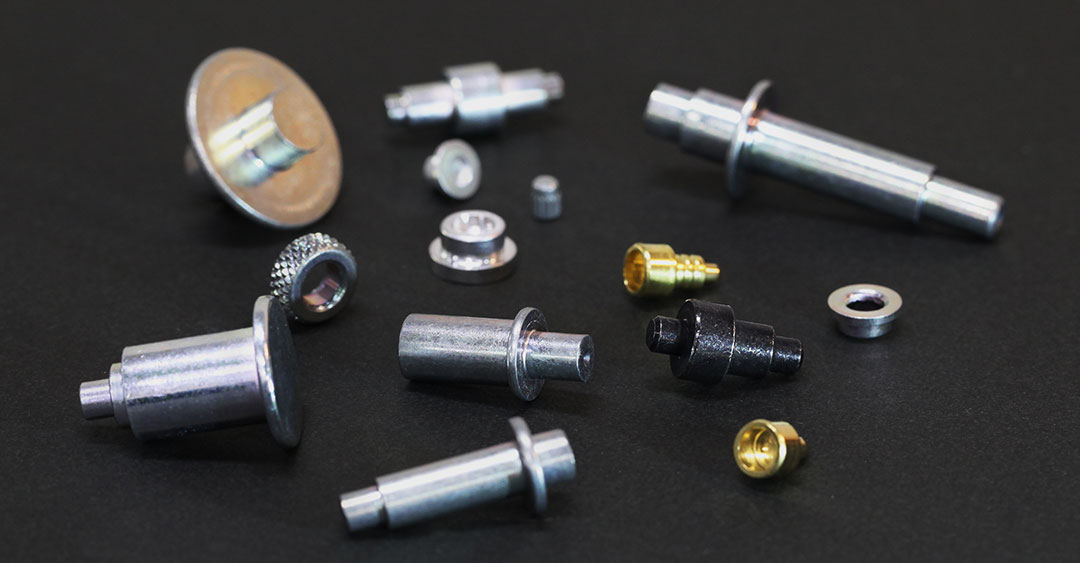
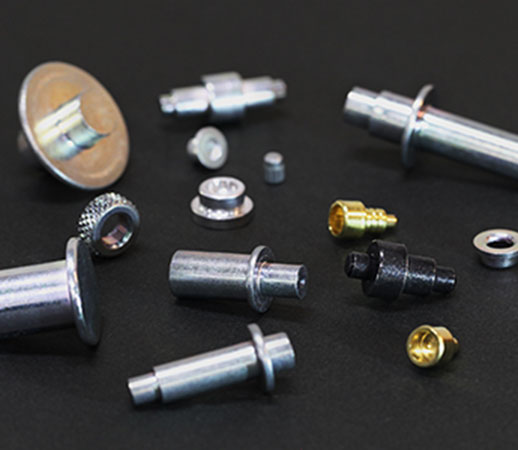
Kofuseibyo provides specially-shaped parts tailored explicitly to drawings and specifications of customers. Total in-house designing and manufacturing heading die is implemented in all the factories in Japan and Thailand. Along with making parts through heading, we make sure of secondary processing through rolling and cutting headed blanks. We have mainly been involved in manufacturing parts designed for electrical and electronic equipment over four decades: audio-visual appliances such as videocassette recorders between the 1980s and the 1990s, and hard disk drives, mobile devices and electronic devices since the 2000s. This accumulated, rich experience allows the production of precision, micro parts to be our dominant field. In recent years, more processable sizes have become available with a new machine, and we are engaged in manufacturing not only precision, micro parts but automotive parts and housing equipment parts. All parts are finished with aftertreatment through heat treatment and plating of processed parts according to the requirements of our customers.
-
Product Samples
-
Use for: Automotive Material: SWCH -
Use for: Automotive Material: Chromoly -
Use for: Automotive Material: Chromoly -
Use for: Automotive Material: SWCH -
Use for: Automotive Material: SWCH -
Use for: Automotive Material: SWCH -
Use for: Automotive Material: SWCH -
Use for: Automotive Material: SWCH -
Use for: Automotive Material: Brass -
Use for: Automotive Material: Brass -
Use for: Automotive Material: Aluminum -
Use for: Automotive Material: Aluminum -
Use for: Automotive Material: Brass -
Use for: Electrical and Electronic Material: Stainless Steel -
Use for: Electrical and Electronic Material: Copper -
Use for: Electrical and Electronic Material: SWCH -
Use for: Electrical and Electronic Material: SWCH -
Use for: Electrical and Electronic Material: SWCH -
Use for: Electrical and Electronic Material: Brass -
Use for: Electrical and Electronic Material: Copper -
Use for: Electrical and Electronic Material: Soft Magnetic Iron -
Use for: Electrical and Electronic Material: Soft Magnetic Iron -
Use for: Housing Equipment Material: SWCH -
Use for: Housing Equipment Material: Aluminum
Miniature Screws (Micro Size Screws)
-
-
Miniature screws are always well-known parts in some certain fields such as watch making but lack versatility and mass marketing that make it difficult to have them on retail sale or to find a manufacturer with technical capabilities. Kofuseibyo leverages its experience to keep miniature screws measuring 0.5 to 1.0 mm in nominal diameter in stock, allowing small-lot retail customers to purchase them off the shelf. We also accept enquiries regarding shipping overseas.
-
-
Materials
-
Processable Material Diameter
Dia. 0.4 mm - Dia. 14.0 mm
-
Main Materials
〔Steel〕 Steel Wire Cold Heading (SWCH), Alloy Steel Wire (SCM), Stainless Steel Wire (SUS XM7, SUS 430, SUS 410)
〔Nonferrous〕 Aluminum Wire (A1100W, A5052W), Copper Wire (C1020W, C1100W), Brass Wire (C2700W) -
-
Secondary Processing
-
Main Processing Methods
- Rolling
- Tapping
- Cutting
-
-
-
After-Treatments
Main Heat Treatments
- Carburizing
- Gas Soft Nitriding
- Quenching and Tempering
- Various Annealing
- Vacuum Heat Treatment (Quenching and Tempering, Various Annealing)
Main Surface Treatments
- Zinc Trivalent Chromate (White)
- Zinc Trivalent Chromate (Black)
- Electro Nickel
- Electroless Nickel
- Electroless Nickel-PTFE
- Black Oxide
- Passivation
- Chemical Polishing
- SS Black
- Various Looseness Preventive Glue
*Heat treatments and Surface treatments are outsourcing.
-
Equipment
Production Equipment
We are fully equipped with headers, from 1 Die 2 Blow (double header) to Parts Former multistage header, along with main 2 Die 3 Blow to satisfy customer needs. Our wide selection of headers allows us to cater to various sizes, from 14-mm-dia automotive parts to 2-mm-dia electrical and electronic equipment parts and less than 1-mm-dia miniature screws. We are also outfitted with the rolling machine, tapping machine, and CNC lathe machine to apply secondary processing, rolling, tapping, and cutting to headed blanks. Original rolling machines are also installed.
Heading Machine (Parts Former) 6 Heading Machine (Header) 42 Rolling Machine 43 Tapping Machine 3 CNC Lathe Machine 5 -
5 Die 5 Blow Parts Former
-
2 Die 3 Blow Header
-
1 Die 2 Blow Header
-
Rolling Machine (Manufacturing In-House)
Main Machine Work Equipment
Equipment for manufacturing die of heading.
Die-sinking Electrical Discharge Machine 3 Wire-cut Electrical Discharge Machine 1 CNC Lathe Machine 1 Abrasive Flow Machine 1 Surface Grinding Machine 4 Cylindrical Grinding Machine 2 -
Die-sinking Electrical Discharge Machine
-
Wire-cut Electrical Discharge Machine
-
CNC Lathe Machine
Main Measuring Equipment
Original inspection sorting machines are capable of inspection of critical control points to parts specifications, coupled with product inspection by general measuring equipment such as a tool microscope. In-house manufacturing of equipment including inspection sorting machines enables us to deliver products that are directed toward a broad spectrum of customer needs.
-
Measuring Microscope
-
Contour Form Measurement Machine
-
Image Dimension Measurement Machine
-
Image Sorting Machine (Manufacturing In-House)
-
-
FAQ
Click below for Frequently Asked Questions (FAQ).
-
Process Flow Chart of Heading Parts
-
What is Heading?
This is a metalworking process that reshapes metal material into a specified form using a die for plastic deformation.
Heading is a metalworking process that reshapes metal material into a specified form using a die for plastic deformation. Which is commonly used in producing general screws compliant with the JIS standard. And heading is analogous to forging. Heading at regular temperatures is called cold heading while heading via the heating of metal is called hot heading. Kofuseibyo adopts cold heading. Coiled wire is used in the heading process. The wire is inserted into a die and pressed with a punch to perform the upsetting, forward extrusion, and backward extrusion process.
-
-
Regarding Heading Machines
The expressions 1 Die 2 Blow and 2 Die 3 Blow are found in our website. The terms refer to the capability of headers, which means how many die shapes the header uses. A 1 Die 2 Blow header inserts workpiece into one die shape and strikes it with two different punches. A 2 Die 3 Blow header inserts workpiece into two die shapes and strikes it with three different punches. There are 5 Die 5 Blow and 8 Die 8 Blow headers capable of using many die shapes. The complexity of the parts being made rises with the number of die shapes, but so does the production cost. Heading machinery is commonly referred to as the header or parts former. There is no definite difference between the names, but parts former appears to be used more for heading machinery that can use many die shapes.
-
What is Rolling?
The rolling process reshapes blanks in dies via plastic deformation by spinning them within the dies.
The rolling process reshapes blanks in dies via plastic deformation by spinning them within dies. This process is used to production screw products. Parts are not always created through rolling alone. Blanks formed through other processes (cold heading in the case of Kofuseibyo) are also used in secondary processes. Examples include the screw thread, groove, knurling, and rounded end. There are a few different rolling methods, but the process used at Kofuseibyo involves flat dies method.
-
Screw Thread
-
Rounded End
-
Knurling (Diamond Pattern)
-
Knurling (Straight Pattern)
-
Groove
-
-
How are screws manufactured?
Here is the heading process using general cross recessed head screws.
-
1. The wire is inserted into the heading machine.
-
2. The wire is cut inside the machine.
-
3. The pre-forming process is performed.
-
4. The finish-forming process is performed. (A cross recess is formed in the head of a workpiece with the this strike to bring the headed blank to finished form)
-
5. The screw thread is shaped through the rolling process.
-
-
What are the advantages and disadvantages of heading?
Advantages
*Appropriate for mass production as a high processing speed allows for superior productivity.
*Possible to produce in large volumes using fewer machines.
*Almost no material is wasted as it is not cutting and therefore very little scrappage is created.
*Parts can be produced more cheaply than through other methods by aligning their specifications and requested amounts with the conditions and advantages of the process.
*The product is strengthened through work hardening (strengthening of metal by plastic deformation) and the absence of fiber material (fiber flow) cutting.Disadvantages
*Must use of die entails initial costs and time for trial production.
*Machine setup and adjustments are time-consuming because headers are not computer numerically-controlled.
*All processes, from materials to aftertreatment, are designed for mass production, which is disadvantageous for small batch production.
*Physical limits to how materials can be reshaped by processing restrict shape and dimensional accuracy.
Heading parts similar to those shaped by the CNC lathe cutting process. The two processes can be compared on the following items. -
What is your minimum order volume for heading parts?
We are flexible in response to customer demands.
We are flexible in response to customer demands, and an order volume will also vary with parts size. The empirical data shows that parts are desirably ordered by tens of thousands per month as a guide, to capitalize on the strengths of the heading process. However, we are adaptable to high-mix low-volume production and still happy to prepare parts to customer needs even if an order is below the guide. If your monthly consumption of parts is low, orders can be placed in bulk allowing a single production volume to be high for an alternative. Please feel free to contact us for details.
-
What types of materials does Kofuseibyo use?
We most commonly use a steel for cold Heading called SWCH (Steel Wire Cold Heading).
We most commonly use a steel for cold heading called SWCH (Steel Wire Cold Heading). Depending on customer specifications, we may also use other materials including stainless steel for corrosion resistance, copper or brass for conductivity, or aluminum for lightness.
-